Ansys Pressure Vessel Pdf Printer
- Ansys Pressure Vessel Pdf Printer Software
- Axisymmetric Analysis In Ansys Apdl
- Hoop Stress In Ansys Workbench
This tutorial is an educational tooldesigned to assist those who wish to learn how to use the ANSYS finiteelement software package. It is not intended as a guide for determiningsuitable modelling methods or strategies for any application. Theauthors of this tutorial have used their best efforts in preparing thetutorial. These efforts include the development,research and testing of the theories and computational models shown in the tutorial.
Trivial pursuit unlimited pc ita youtube. Submitted on 8/9/2017 Review title of BryanStop asking me to review itFeel like I bought the app twice:(I guess buy the $3.99 version to start.
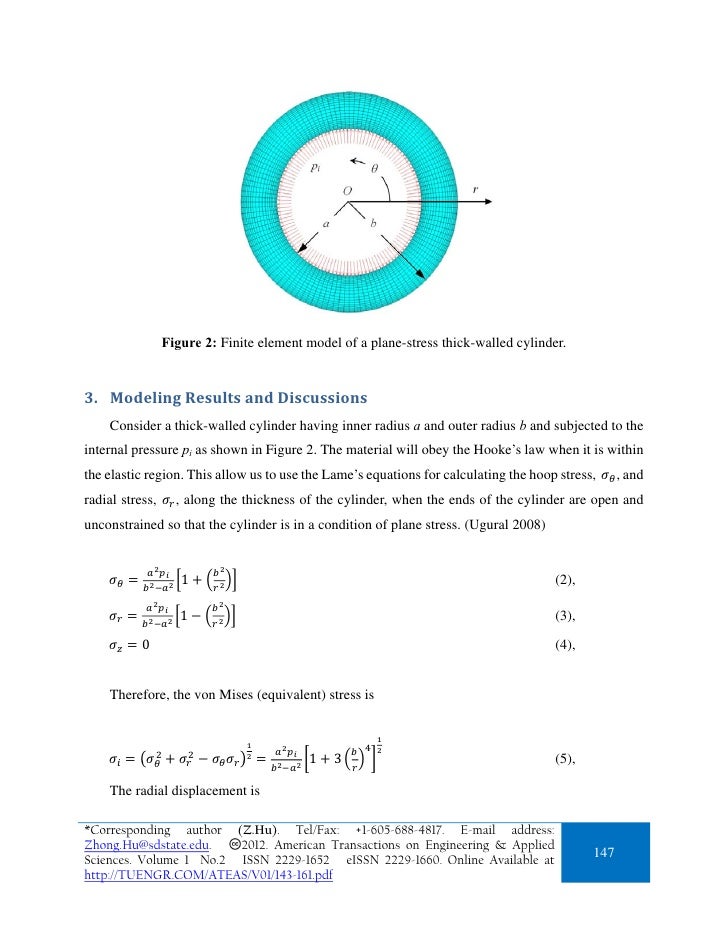
The authors make no warranty of any kind, expressed orimplied, with regard to any text or models contained in this tutorial. Figure 1: Details of the Pressure Vessel - all dimensions in mm.Thereare standard theories available for the behaviour of thin andthick walled cylinders subjected to internal pressure. These equationscan befound in any text book on mechanics of solids or in any reference book.We can use these theories to predict the expected stresses in thepressure vessel due to the applied loading. The calculations for thevarious stresses is shown on pages 328 to 329 of Practical Stress Analysis with Finite Elements (2nd Ed)by Bryan J. Mac Donald and is summarised in the table below. Step 7: Apply the Boundary Conditions.Although the solver already knows that we are performing an axisymmetric analysis due to an axisymmetric element being used, we still need to place a symmetry constraint on the edges of the model that touch the Y-axis.Preprocessor Loads Define Loads Apply Structural Displacement Symmetry B.C.
On Lines pick the lines on the axis of symmetry (i.e.You will probably get a warning saying that ' Bothsolid model and finite element boundary conditions have been applied tothis model. As solid loads are transferred to the nodes or elements,they can overwrite directly applied loads'. This is OK just click on Close to dismiss this dialog.Step 8: Apply the Internal Pressure Load. In the Main Menu click on Preprocessor Loads Define Loads Apply Structural Pressure On Lines.Click on all the lines representing the internal wall of the pressure vessel and then click on OK in the picker dialog box.
The 'Apply Pres on a Line' dialog box will now appear. Enter 10000 as the pressure value as shown below. Step 9: Solve the Problem.In the Main Menu select Solution Analysis Type New Analysis.Make sure that Static is selected in the dialog box that pops up and then click on OK to dismiss the dialog.Select Solution Solve Current LS to solve the problem.Anew window and a dialog box will pop up. Take a quick look at theinfromation in the window ( /STATUS Command) before closing it.Click on OK in the dialog box to solve the problem.Once the problem has been solved you will get a message to say that the solution is done, close this window when you are ready.Step 10: Examine the Results.In the Main Menu select General Postproc Plot Results Deformed Shape.
Ansys Pressure Vessel Pdf Printer Software
Select Def + undef edge in order to show both the deformed and undeformed shapes.Your screen should look something like this. It is clear that the side wall of the pressure vessel has slightly 'bowed' out due to the internal pressure. The end caps have significantly deformed in comparison to the side wall.
The maximum displacement is, however, approximately 2 x 10 -6 m which is well below the yield stress for steel - meaning our assumption of a linear elastic material is valid. Note that ANSYS, by default, will exaggerate any deformation by scaling it up in order to make it obvious.Now let's examine the principal stresses: General Postproc Plot Results Contour Plot Nodal Solu Stress 1st Principal Stress, click on OK to display the plot, which should look like this. The first principal stress is the Hoop Stress and we are expecting a value of approximately 55,000 Pa based on our analytical calculations.
Clearly something is wrong with this plot. We are seeing very large stress concentrations at the sharp corner where the end caps join the side wall. It is likely that the stress in the side wall itself is quite close to the predicted analytical value. Let's investigate this by only displaying results for the elements at the middle of the vessel side wall:. Utility Menu Select Entities.
In the 'Select Entities' dialog box that appears make sure that 'Elements' is selected in the top box and then click on OK. SummaryThis tutorial has given you the following skills:. The ability to model axisymmetric problems in ANSYS. The ability to select a subset of a finite element model and only examine the result for that subset. Experiencein comparing the results obtained from your finite element model withother results and validating your results against the other results.Log Files / Input FilesThelog file for this tutorial may also be used as an input file toautomatically run the analysis in ANSYS.
Axisymmetric Analysis In Ansys Apdl
In order to use this file as aninput file save it to your working directory and then select Utility Menu File Read input from. andselect the file. You should notice ANSYS automatically building thefinite element model and issuing all the commands detailed above.Quitting ANSYSTo quit ANSYS select Utility Menu File Exit. In the dialog box that appears click on Save Everything (assuming that you want to) and then click on Ok.
Authors: Sebastien Lachance-Barrett and Vincent PrantilPhysics SetupHere are the boundary conditions we will impose on the model:Symmetry boundary condition at the top edge implies zero displacement in the axial (y) direction. The top edge represents a plane of symmetry since it is located at the mid-length of the cylinder and we are modeling only half the length. In ANSYS, we impose this symmetry boundary condition using a “Frictionless support”.In an axisymmetric model, no displacement constraints are necessary in the radial direction to prevent rigid body motion in that direction. This is because radial displacement represents expansion/contraction of the structure which is resisted structurally.The following video shows how to specify the physics of the problem: axisymmetric analysis, material properties (Young's modulus and Poisson ratio) and boundary conditions.
Hoop Stress In Ansys Workbench
These settings get fed into the element formulation when obtaining the numerical solution later.Note: We perform an axisymmetric analysis by clicking on Geometry, expanding Definition, and selecting Axisymmetric for the 2D behavior.